- Home
- Manufacturing Technologies
What are the Manufacturing Technologies?
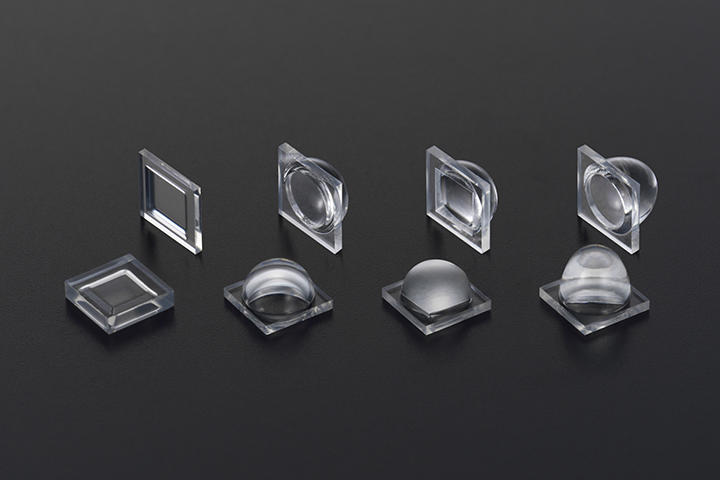
Advanced Manufacturing Technologies for LED Lenses
With the rapidly evolving era of LED lighting, performance, efficiency, and lifespan heavily rely on the quality and precision of LED lenses. At Krishani LED Lenses, we combine cutting-edge manufacturing technologies and decades of optical engineering expertise to deliver lenses that raise the bar for performance across industries. In this article, we explore how cutting-edge processes like LED lens molding, CNC machining, and 3D printing enable us to push optical design to new extremes. It highlights how our state-of-the-art methods ensure unparalleled control over light, increased efficiency, and outstanding durability in a range of industries, from automotive lighting to medical devices.
Why Manufacturing Precision Matters in LED Lenses?
LED lenses convert raw light into managed light, removing glare, increasing the uniformity of colors, and projecting beams with millimeter-level precision. Achieving this precision demands some seriously advanced manufacturing technologies. With the industry increasingly calling for smarter, more efficient lighting, precision optics has become the foundation of innovative LED lens production.
Precision optics aren't so much about precision as they are about optimizing performance on a microscopic scale. Every millimeter of curve, every angle degree, and every deviation in material transparency directly impact the output of an LED light. Precision optics make lenses focus light along precise, calculated paths. That means consistent light diffusion, minimal glare, and peak energy efficiency. LED lenses are required to direct and maximize the light output, ensuring:
- Better light quality for spaces such as hospitals or art galleries.
- Enhanced vehicle safety and street illumination where beam accuracy is crucial.
- Improved efficiency in industrial and commercial areas with focused lighting requirements.
Core Technologies for LED Lens Manufacturing
1. LED Lens Molding
At Krishani, we use advanced techniques and strict quality control procedures to ensure our lenses are of superior quality. LED lens molding is a process whereby optical-grade plastic or silicone is injected or compressed into a mold to form the shape of the end lens. We employ both injection molding and compression molding processes depending on different material requirements and end-use applications.
A. Injection Molding for Optics
For mass production where accuracy is the top priority, we use injection molding. This method is the most efficient and accurate method of molding, making it perfect for creating large volumes of LED lenses with accurate dimensions. This involves injecting molten, high-quality polymers like PMMA (polymethyl methacrylate) or polycarbonate into a mold cavity under strictly controlled conditions. Our injection molding for optics ensures:
- High repeatability
- Material versatility
- Design Versatility
- Optical uniformity
- Dimensional accuracy
B. Compression Molding for Silicone Lenses
Compression molding is especially suited for manufacturing silicone-based lenses, which are both temperature-resistant and flexible. Unlike injection molding, compression molding involves filling premeasured liquid silicone rubber (LSR) into the mold cavity. Our expertise in this technique produces lenses that are not only optically excellent but also mechanically robust. We use this molding method for silicone lenses, which provides:
- High thermal stability (up to 200°C)
- Better optical clarity
- Flexibility for intricate shapes
- Impact resistance and durability
- UV and chemical resistance
2. CNC Machining for LED Lenses
CNC (Computer Numerical Control) machining uses computer-controlled, automated tools to machine lenses out of solid blocks of optical-grade material. The CNC machining for LED Lenses is used for its unparalleled flexibility and micron-level precision, making it perfect for prototyping and custom designs. Subtractive in nature, this method provides phenomenal control over size and is ideal for high-performance or non-standard LED lens applications. Our CNC capabilities include:
- Multi-axis machine tools.
- Cutting tools with diamond tips for an incredibly smooth finish.
- Smart control systems to correct errors in real time.
- Polishing tools to provide crystal clear machined lenses.
3. 3D Printing of Optical Components
3D printing allows us to test a variety of lens designs before finalizing mold manufacture or CNC milling. This method lets us rapidly produce prototype lenses that can be checked for fit, size, and basic light control features. This significantly cuts down on the chances of costly errors and speeds up the product development process. Here are some of the main advantages of 3D printing: Quick changes can be made for faster development Affordable than traditional prototyping methods Risk reduction early on before costly tooling Freedom to design complex shapes.
Optical Lens Manufacturing Process at Krishani
Krishani specializes in manufacturing optical lenses with a focus on precision, scalability, and ensuring customer satisfaction. Every stage of the process is carefully planned to transform initial concepts into top-notch LED lenses, with each item rigorously tested to align with both industry regulations and the unique requirements of our clients. Our efficient workflow includes:
- Client Consultation: We start by understanding your need for lenses, digging into the optical, mechanical, and thermal specifications.
- Design & Simulation: We use advanced CAD modeling and optical simulation tools to figure out the best design for feasibility and peak performance.
- Prototyping: We then make some prototypes by using 3D printing or CNC machining to achieve a practical experience of the design.
- Tooling & Mold Development: We create very accurate molds which are exactly suited to the specific design and material of your lens.
- Mass Production: Depending on the usage, we develop your lenses in quantity through injection molding, compression molding, or CNC machining.
- Post-Processing: We apply any necessary coatings, polish the lens surfaces to perfection, and perform any needed curing steps.
- Quality Control: We meticulously inspect every lens using top-of-the-line metrology equipment to ensure the highest quality.
- Packaging and Logistics: Finally, we pack and ship your lenses to you safely and efficiently.
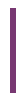
Why Choose Krishani LED Lenses?
At Krishani LED Lenses, we are driven by core values that guide our business and define our commitment to our clients.

Expertise and Experience - With years of experience in the optical and lighting industries, we have the expertise to deliver custom-designed solutions that meet the most demanding requirements.

High-Quality Products - Our lenses are made from high-quality materials, ensuring durability, clarity, and long-lasting performance.

Custom Solutions - We specialize in providing tailored LED lens solutions that meet the unique needs of our clients.

Exceptional Customer Service - We provide end-to-end support, from initial consultation to post-delivery assistance, ensuring our clients are delighted with the results.
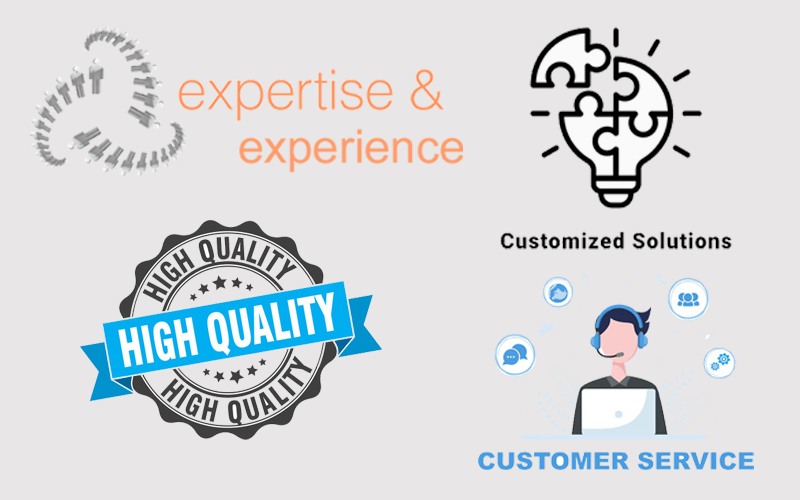
Your Trusted Partner in Optical Excellence
Krishani is a pioneer in the art of manufacturing LED lenses, using precision technologies like injection molding, CNC machining, and 3D printing with finesse. We are here to provide customized solutions, technical assistance, and end-to-end manufacturing services. You're looking for a new product or need to produce in high quantities, we're here to help you. Contact us now at +1 917-730-4350 or info@krishaniledlenses.com to witness unparalleled quality and service in the production of LED lenses.
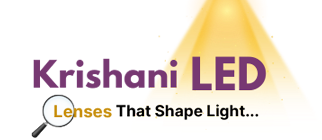
Ready to See your Idea into Reality
We have served 157+ Clients so far… Discuss your Requirements with Our Experts.

